4.9. Центр днища резервуара должен быть зафиксирован приваренным к нему знаком с отверстием 10 мм в центре.
4.10. При монтаже стенки резервуаров следует обеспечить ее устойчивость, а также не допускать сминания днища и нижней кромки рулона стенки.
4.11. Врезка и приварка патрубков резервуарного оборудования на I, II и III поясах, а также оборудования, устанавливаемого на днищах, понтонах и плавающих крышах, должны быть закончены до гидравлического испытания резервуара.
4.12. Вертикальность стенки резервуара, не имеющего верхнего кольца жесткости, в процессе монтажа должна контролироваться не реже чем через 6 м, а резервуара, имеющего кольцо, - при установке каждого монтажного элемента кольца.
Испытание конструкций и приемка работ
4.13. Испытание резервуаров должно производиться наливом его водой до высоты, предусмотренной проектом.
4.14. Перед проведением испытаний весь персонал, принимающий участие в них, должен пройти инструктаж.
На все время испытаний устанавливается граница опасной зоны с радиусом не менее двух диаметров резервуара, внутри которой не допускается нахождение людей, не связанных с испытанием.
Во время повышения давления или вакуума допуск к осмотру резервуара разрешается не ранее чем через 10 мин после достижения установленных испытательных нагрузок.
Во время испытаний запрещается оставлять без наблюдения герметически закрытые резервуары, не имеющие соответствующей дыхательной аппаратуры. Контрольные приборы следует располагать в соответствии с п. 5.23 настоящей главы.
4.15. При испытании резервуаров низкого давления принимается размер избыточного давления на 25%, а вакуум на 50% больше проектной величины, если в проекте нет других указаний.
Примечание. При отсутствии гибкого участка трубопровода первая опора со стороны резервуара должна устанавливаться после окончания гидравлических испытаний.
4.16. Испытание резервуаров повышенного давления производится в соответствии с требованиями, приведенными в проекте, с учетом их конструктивных особенностей.
4.17. При обнаружении течи из-под края днища или через контрольные трубки, появления мокрых пятен на поверхности отмостки испытание необходимо прекратить, слить воду. устранить причину течи.
При обнаружении трещин в швах поясов корпуса испытание должно быть прекращено и вода слита до уровня:
на один пояс ниже расположения трещин - при обнаружении трещин в поясах от I до IV;
до V пояса - при обнаружении трещин в поясах VI и выше.
4.18. Гидравлическое испытание рекомендуется проводить при температуре окружающего воздуха +5°С и выше.
Таблица 18
Наименованиe отклонения |
Допускаемое отклонение |
1 |
2 |
Днище |
|
1. Отклонение наружного контура днища от горизонтали |
См. табл. 19 |
2. Высота хлопунов днища (допускаемая площадь одного хлопуна 2 м2) |
Не более 150 мм |
Стенка |
|
3. Отклонение величины внутреннего радиуса стенки на уровне днища от проектной при радиусе: |
|
До 12 м включительно |
± 20 мм |
Свыше 12 м |
± 30 мм |
4. Отклонение высоты стенки от проектной, смонтированной: |
|
Из рулонной заготовки |
± 15 мм |
Из отдельных листов |
± 50 мм |
5. Отклонение образующих стенки от вертикали |
См. табл. 20 |
6. Выпучины или вмятины на поверхности стенки вдоль образующей |
См. табл. 21 |
Понтон и плавающая крыша |
|
7. Отклонение наружного контура понтона или плавающей крыши от горизонтали |
± 20 мм |
8. Отклонение направляющих понтона или плавающей крыши от вертикали |
25 мм |
9. Отклонение наружного кольцевого листа понтона или плавающей крыши от вертикали на высоту листа |
± 10 мм |
Покрытие |
|
10. Отклонение стрелок прогиба радиальных элементов в центре и промежуточных узлах от проектных (с учетом строительного подъема) |
± 0,02 |
11.. Разность отметок смежных узлов радиальных балок и ферм |
10 мм |
Примечание. Нижняя часть наружного контура понтона или плавающей крыши не должна находиться выше уровня жидкости. |
При необходимости испытания резервуаров в зимних условиях водой должны быть приняты меры по предотвращению замерзания воды в трубах и задвижках, а также обмерзания стенок резервуара.
Таблица 19
|
Допускаемые отклонения наружного контура днища, мм |
Емкость резервуара, м3 |
при незаполненном резервуаре |
при заполненном резервуаре |
|
разность oтметок соседних точек на расстоянии 6 м |
разность отметок любых других точек |
разность oтметок соседних точек на расстоянии 6 м |
разность отметок любых других точек |
Менее 700 |
10 |
25 |
20 |
40 |
700 - 1000 |
15 |
40 |
30 |
60 |
2000 - 5000 |
20 |
50 |
40 |
80 |
10000-20000 |
10 |
50 |
30 |
80 |
Таблица 20
Резервуар |
Допускаемые отклонении, образующих стенки от вертикали, мм |
|
N поясов |
|
I |
II |
III |
IV |
V |
VI |
VII |
VIII |
IX |
X |
XI |
XII |
С понтонами или плавающими крышами |
Для резервуаров высотой до 12 м |
|
10 |
20 |
30 |
40 |
45 |
50 |
55 |
60 |
-- |
-- |
-- |
-- |
|
Для резервуаров высотой до 18 м |
|
10 |
20 |
30 |
40 |
45 |
50 |
55 |
55 |
55 |
55 |
60 |
60 |
Другие типы |
Для резервуаров высотой до 12 м |
|
15 |
30 |
40 |
50 |
60 |
70 |
80 |
90 |
-- |
-- |
-- |
-- |
|
Для резервуаров высотой до 18 м |
|
15 |
30 |
40 |
50 |
60 |
60 |
70 |
70 |
70 |
80 |
80 |
90 |
Примечания:1. Замеры производятся для каждого пояса на расстоянии до 50 мм от верхнего горизонтального шва.
2. Проверка отклонений производится не реже чем через 6 м по окружности резервуара.
3. Для 20% образующих (по которым производится контроль отклонений) резервуаров с понтонами или плавающими крышами допускаются в уровне восьмого пояса отклонения 90 мм, а для резервуаров других конструкций 120 мм. В уровне остальных поясов допускаемое отклонение определяется по интерполяции.
4. При определении отклонений учитывается телескопичность стенки резервуаров, смонтированных полистовым способом. |
4.19. Резервуар считается выдержавшим гидравлическое испытание, если в процессе испытания и по истечении 24 ч на поверхности корпуса резервуара или по краям днища не появятся течи и если уровень воды не будет снижаться.
Обнаруженные мелкие дефекты (свищи, отпотины) подлежат исправлению при пустом резервуаре. Исправленные места должны быть проверены на герметичность.
4.20. Отклонения геометрических размеров и формы стальных конструкций резервуаров от проектных не должны превышать величин, приведенных в табл. 18, 19, 20 и 21.
Таблица 21
Расстояние от нижнего до верхнего края выпучины или вмятины, мм |
Допускаемая величина выпучин или вмятин на поверхности стенки вдоль образующей, мм |
До 1500 включительно |
15 |
Свыше 1500 до 3000 |
30 |
Свыше 3000 до 4500 |
45 |
Примечание: Суммарные отклонения стенки резервуаров должны укладываться в допускаемые отклонения по табл. 20. |
4.21. На резервуар, сдаваемый в эксплуатацию, составляется паспорт согласно прил. 2 настоящей главы.
5. ДОПОЛНИТЕЛЬНЫЕ ПРАВИЛА ДЛЯ КОНСТРУКЦИЙ МОКРЫХ ГАЗГОЛЬДЕРОВ
5.1. Настоящие дополнительные правила должны соблюдаться при изготовлении, монтаже и приемке стальных конструкций мокрых газгольдеров емкостью до 30000 м3 с вертикальными направляющими, включающих следующие элементы:
листовые конструкции резервуара, телескопа и колокола;
внешние и внутренние направляющие телескопа и колокола со связями;
водяные затворы;
стойки и стропила колокола.
ИЗГОТОВЛЕНИЕ
5.2. Изготовление листовых конструкций следует производить, как правило, рулонами и укрупненными габаритными элементами, кроме случаев, предусмотренных проектом.
5.3. Конструкции, приведенные ниже, должны пройти общую сборку или изготовляться по кондукторам:
внешние направляющие со связями; гидрозатворы; стропильные покрытия со связями; балконные площадки с приваренными элементами уторного кольца стенки.
Гидрозатвор должен изготовляться в виде укрупненных отправочных элементов.
5.4. В стропильных ригелях кровли колокола при их изготовлении должен быть предусмотрен строительный подъем, равный диаметра колокола.
5.5. Полотнища днищ и стенок резервуара должны быть изготовлены с выполнением требований п. 4.3 настоящей главы.
Сварка при изготовлении и монтаже
5.6. Стыковые сварные соединения окраек днища должны выполняться на подкладке, не менее чем в два слоя.
5.7. Контроль герметичности всех швов днища и кольцевого таврового шва производится вакуумом, а всех швов прочих частей газгольдера - керосином в соответствии с п. 1.54 настоящей главы.
Просвечиванию проникающими излучениями подлежат все пересечения вертикальных и горизонтальных швов резервуаров в листах толщиной 6 мм и более, а также все стыковые соединения окраек днищ в местах примыкания к ним стенки резервуара. Длина снимка должна быть не менее 240 мм.
Примечание. Взамен просвечивания сварных соединений при толщине стали 10 мм и более разрешается производить контроль ультразвуковой дефектоскопией с последующим просвечиванием проникающими излучениями участков швов с признаками дефектов.
Монтаж
5.8. До начала монтажа конструкций газгольдера должна быть произведена приемка естественного и искусственного оснований, а также гидроизолирующего слоя фундаментов и приямков.
5.9. Отклонения фундаментов газгольдеров от проекта не должны превышать величин, приведенных в табл. 22.
Таблица 22
Наименование отклонения |
Допускаемое отклонение, мм |
1. Отклонение от проекта отметок поверхности кольцевого фундамента, определяемых не реже чем через 6 м и не менее чем в 8 точках |
± 5 |
2. Разность отметок любых не смежных точек кольцевого фундамента, не более |
10 |
3. Отклонение в ширине кольцевого фундамента по верху |
+50; - 0 |
4. Отклонение от проекта наружного диаметра кольцевого фундамента |
+50; - 30 |
5.10. Поверхность искусственного основания под днище резервуара газгольдера должна иметь подъем к центру основания, равный 1/75 диаметра резервуара. Все железобетонные плиты должны иметь тот же уклон, что и искусственное основание.
5.11. Зазоры, образующиеся между поверхностью кольцевого фундамента и днищем, должны заполняться цементным раствором после установки и приварки первого пояса резервуара.
5.12. При монтаже стенок резервуара, телескопа и колокола следует обеспечить их устойчивость.
5.13. Крыше колокола должен быть придан строительный подъем, для чего центральное опорное кольцо стропильных ригелей необходимо установить выше проектного положения (относительно проектной верхней поверхности кольцевого фундамента) на величину, обеспечивающую требование п. 5.4 настоящей главы.
5.14. При монтаже кровли колокола нельзя допускать размещение на ней каких-либо грузов, а также скопления снега.
5.15. Приварка внешних направляющих (с площадками и связями, молниеприемниками и роликами объемоуказателей) должна производиться только после полной сборки и проверки прямолинейности каждой направляющей в отдельности, а также выверки правильности геометрического положения всех направляющих.
5.16. При укладке грузов, предназначенных для обеспечения принятого в проекте давления газа, суммарная фактическая их масса, определяемая контрольным взвешиванием, и фактическая масса подвижных секций газгольдера, определяемая по исполнительным чертежам, не должна расходиться с проектом более чем на 2%.
Испытание конструкций и приемка работ
5.17. Отклонения геометрических размеров и формы стальных конструкций мокрых газгольдеров не должны превышать величии, приведенных в табл. 23.
5.18. До сдачи в эксплуатацию каждого газгольдера должна быть произведена его техническая приемка:
а) внешний осмотр газгольдера и проверка его размеров;
б) испытания отдельных узлов и элементов;
в) гидравлическое испытание резервуара и газовых вводов;
г) испытание газгольдера в целом.
5.19. Испытание на герметичность днища резервуара, настила кровли и гидрозатворов колокола и телескопа следует производить до испытания резервуара газгольдера наливом воды.
5.20. Испытание настила кровли на герметичность (предварительное) производится путем создания внутреннего давления воздухом в период подъема колокола и нанесения мыльного раствора на сварные соединения снаружи.
Обнаруженные при испытании дефекты швов кровли должны быть устранены подваркой без вырубки дефектных мест.
Таблица 23
Отклонение |
Допускаемое отклонение |
1. Разность двух любых радиусов резервуара, телескопа и колокола |
Не более 20 мм |
2. Отклонение стенок резервуара от вертикали на каждый 1 м высоты стенки |
3 мм |
3. Отклонение высоты резервуара от проекта |
± 20 мм |
4. Отклонение радиуса горизонтальных колец гидрозатвора телескопа и колокола |
± 10 мм |
5. Отклонение зазора между поверхностями гидрозатвора колокола и телескопа |
± 20 мм |
6. Отклонение от проекта горизонтального размера в свету между поверхностью верхнего листа стенки телескопа и внешней гранью горизонтального листа затвора колокола, а .также между вертикальной поверхностью затвора телескопа и внешней поверхностью |
± 8 мм |
7. Отклонение от вертикали внутренних направляющих телескопа и стоек колокола (после окончания сварки) на всю высоту |
10 мм |
8. Отклонение стропил кровли колокола из вертикальной плоскости |
1/1000 диаметра колокола |
9. Отклонение от центра кровли оси каждого стропильного ригеля (в плане) |
10 мм |
10. Отклонение внешних направляющих от вертикали (на всю высоту направляющих): |
10 мм |
в радиальном направлении |
10 мм |
в плоскости, касательной к цилиндрической поверхности газгольдера |
15 мм |
После исправления дефектных участков швов они должны быть подвергнуты повторному испытанию.
5.21. Испытание на герметичность гидрозатворов телескопа и колокола должно производиться керосином до покраски газгольдера и установки грузов.
5.22. До начала испытания резервуара все газопроводы должны быть продуты.
Испытание резервуара производится наливом воды на высоту, предусмотренную проектом. Налив воды осуществляется ступенями по поясам с промежутками времени, необходимыми для осмотра конструкций.
Гидравлическое испытание рекомендуется проводить при температуре окружающего воздуха +5°С и выше. При необходимости испытания газгольдеров в зимних условиях должны быть приняты меры по предотвращению замерзания воды в трубах и задвижках, а также обмерзания стенок резервуара, колокола, телескопа.
5.23. Перед проведением испытаний резервуара наливом воды все работники, принимающие участие в испытаниях, должны пройти инструктаж.
На все время испытаний устанавливаются границы опасной зоны с радиусом не менее двух диаметров газгольдера, внутри которой не допускается нахождение людей, не связанных с испытаниями.
Во время повышения уровня воды в резервуаре лица, назначенные для осмотра конструкций, должны находиться вне границ опасной зоны или в надежных укрытиях.
Контрольные приборы, за которыми производится постоянное наблюдение в течение всего времени испытаний, должны устанавливаться вне опасной зоны или в надежных укрытиях.
5.24. При выявлении трещин в швах поясов корпуса испытание приостанавливается и уровень воды снижается:
на один пояс ниже расположения трещины - при обнаружении трещин в поясах I - VI;
до V пояса - при обнаружении трещин в поясах VII и выше.
Одновременно производится проверка герметичности сварных швов на газовых вводах. В процессе испытания резервуара должны быть обеспечены условия, исключающие образование вакуума в колоколе.
5.25. После исправления всех дефектов резервуара и газовых вводов составляются соответствующие акты.
5.26. До начала испытания газгольдера в целом необходимо выполнить подготовительные работы, необходимые для производства соответствующих замеров. Антикоррозионная защита производится после испытания.
5.27. Испытание газгольдера в целом производится путем налива воды и нагнетания воздуха, при этом:
а) во время подъема колокола необходимо следить за показанием манометра и горизонтальностью подъема; в случае резкого увеличения давления подъем колокола должен быть прекращен и после выявления и устранения причин, задерживающих движение колокола, разрешается производить его дальнейший подъем;
б) первый подъем колокола и телескопа следует производить медленно до момента, когда воздух начнет выходить через автоматическую свечу сброса газа в атмосферу;
в) одновременно с подъемом колокола производится проверка герметичности швов листового настила кровли;
г) после этого опускают колокол и телескоп, производя проверку их герметичности обмыливанием швов обшивки телескопа и колокола; подварку неплотностей производят после полного опускания телескопа и колокола;
д) затем несколько раз колокол и телескоп поднимают и опускают с большей скоростью, чем первый раз, после чего колокол или телескоп частично опускают в воду с таким расчетом, чтобы объем воздуха составлял 90% номинального объема газгольдера, и в таком положении производится семисуточное испытание газгольдера.
При испытании нельзя допускать образования вакуума.
5.28. Утечка воздуха после семисуточного испытания газгольдера определяется как разность между нормальным (V0) и измеренным (Vt) объемами воздуха. Нормальный объем воздуха определяется по формуле
(3)
где V0 - нормальный объем сухого воздуха в м3 при температуре 0°С и нормальном давлении 760 мм рт. ст.;
Vt - измеренный объем воздуха в м3 при средней температуре t°, барометрическом давлении В мм рт. ст. и среднем давлении воздуха в газгольдере Р мм рт. ст.;
Рпар - парциальное давление водяных паров, находящихся в воздухе при температуре t° и давлении В мм рт. ст.;
t° - средняя температура воздуха в °С, определяемая как среднее арифметическое замеров температур в разных местах над крышей колокола (не менее трех).
При незначительной разнице температур в начале и конце испытания величина Рпар может не учитываться. В этом случае вычисление производится по формуле
(4)
5.29. В процессе испытания ежедневно в 6 - 8 ч утра должны производиться контрольные промежуточные замеры и определения утечек воздуха. Дежурства людей при этих испытаниях должны быть круглосуточными.
5.30. Определенная в конце испытания утечка воздуха должна быть пересчитана на соответствующую утечку газа путем умножения величины утечки воздуха на величину , где - удельные веса соответственно воздуха и газа.
5.31. Газгольдер считается выдержавшим испытание на герметичность, если полученная в результате пересчета величина утечки газа при непрерывном испытании за семь суток не превышает 3% для газгольдеров емкостью до 1000 м3 включительно, и 2% для газгольдеров емкостью 3000 м3 и выше.
Величина утечки относится к номинальному объему газгольдера. О результатах испытания составляется соответствующий акт с участием заказчика.
5.32. В заключение газгольдер испытывается быстрым (от 1 до 1,5 м в 1 мин) двукратным подъемом и опусканием подвижных частей.
При подъеме и опускании перекос корпуса колокола и телескопа не должен превышать от уровня воды 1 мм на 1 м диаметра колокола и телескопа.
Отверстия в настиле кровли колокола и иных местах установки испытательных приборов завариваются с помощью круглых накладок с проверкой швов на плотность. Пазы резервуаров после окончания испытания газгольдера пломбируют, а смотровые люки колокола оставляют открытыми.
5.33. На газгольдер, сдаваемый в эксплуатацию, следует составить паспорт согласно прил. 3 к настоящей главе.
6. ДОПОЛНИТЕЛЬНЫЕ ПРАВИЛА ДЛЯ КОНСТРУКЦИЙ МАЧТОВЫХ И БАШЕННЫХ СООРУЖЕНИЙ
6.1. Настоящие дополнительные правила должны соблюдаться при изготовлении, монтаже и приемке стальных конструкций мачтовых и башенных сооружений объектов радиосвязи, радиовещания и телевидения.
ИЗГОТОВЛЕНИЕ
6.2. Внутренние поверхности труб перед обработкой и установкой заглушек должны быть очищены от пыли и грязи, а труб, открытых с торцов, диаметром 250 мм и выше должны быть огрунтованы.
6.3. Стенки отверстий для труб во фланцах и соприкасающиеся плоскости фланцев должны быть механически обработаны (резанием). Зазор между трубой и стенкой отверстия во фланце должен быть 0 - 3 мм при условии совмещения центра фланца с осью трубы.
Механическую обработку сопрягаемых плоскостей фланцев разрешается не производить при условии, если листовая сталь, из которой изготовляются фланцы, выправлена и имеет гладкую поверхность.
6.4. Отверстия для крепления деталей в фасонках оттяжечных узлов мачт, раскосов из круглой стали, распорок, тяг анкерных фундаментов должны образовываться на проектный диаметр по допускам для болтов повышенной точности, приведенным в табл. 5.
6.5. К отправочным элементам мачт и башен на заводе-изготовителе должны быть прикреплены опоры для монтажных кранов, детали для навески подмостей, детали для крепления временных расчалок.
6.6. Швы сварных соединений заглушек трубчатых элементов, узлов примыкания трубчатых раскосов и распорок, а также швы заваренных прорезей в трубчатых конструкциях должны быть выполнены герметичными и испытаны на плотность избыточным давлением воздуха 0,4 кгс/см2. Испытанию подвергаются 5% трубчатых элементов.
В случае обнаружения дефектных швов количество испытываемых элементов удваивается. При обнаружении дефектов в удвоенном количестве элементов испытанию подвергаются все элементы мачты и башни.
Все дефекты, выявленные при испытаниях, устраняются, а отверстия, предназначавшиеся для подачи сжатого воздуха, завариваются герметичным швом после окончания испытаний.
Заглушки труб после испытания элементов на герметичность должны быть покрыты слоем битума № 4.
6.7. Конструкции мачт и башен должны изготовляться по кондукторам, обеспечивающим правильность размеров и взаимозаменяемость элементов, плотное соприкасание обработанных элементов монтажных стыков, а также совпадение отверстий в монтажных стыках и других соединениях.
Конструкции в соответствии с п. 1.29 настоящей главы должны проходить последовательную контрольную сборку всех секций (панелей):
мачты - согласно п. 4 табл. 24 настоящей главы;
башни габаритные - пространственными секциями, негабаритные - плоскостными панелями (допускается сборка до оси симметрии).
Для проверки башен должно быть собрано не менее трех секций.
Конструкции решетчатых матч и башен индивидуального изготовления, выполняемые без применения кондукторов и специальных приспособлений, а также опорные секции мачт со съемными консолями должны подвергаться общей сборке на заводе-изготовителе.
Конструкции листовых трубчатых матч индивидуального изготовления подлежат общей сборке. При общей сборке устанавливаются фиксаторы и наносится продольная ось мачты по образующей цилиндрической поверхности, от которой производится разметка положения всех лацменов, дверей, отверстий и др.
Допускаемые отклонения действительных размеров изготовленных конструкций мачт и башен от проектных не должны превышать предусмотренных в табл. 24. Допускается применение заводских сварных стыков прочностью не ниже прочности свариваемой стали со 100% контролем качества сварных соединений физическими методами.
Таблица 24
Наименование отклонения |
Допускаемое отклонение |
Мачты и башни |
|
1. Разность длин отдельных поясов в одной секции |
базы, но не более 2 мм
|
2. Тангенс угла между фактическим и проектным положениями фланцев поясов |

|
3. Зазоры между фланцами двух смежных секций: |
|
в пределах кольца шириной 20 мм во круг трубы пояса |
0,5 мм |
у наружных кромок между фланцами |
3 мм |
Мачты решетчатые и листовые трубчатые |
|
4. Стрела прогиба оси ствола мачты при общей и контрольной сборке (длина собираемой части не менее расстояния между ярусами оттяжек) |
расстояния между ярусами оттяжек
|
5. Местные искривления образующих трубчатой листовой мачты, измеряемые прямолинейным шаблоном длиной 1 м (искривления и вмятины глубиной до 2 мм не учитываются) |
1/50 длины искривленного участка, но не более 0,5 толщины стенки трубы |
6. Чернота отверстий для болтов во фланцевых соединениях при общей или контрольной сборках |
1,5 мм |
7. Угол между фактическим и проектным положениями фасонки для крепления оттяжек решетчатых и трубчатых мачт |
1° |
8. Разность в толщине фасонок в одном фланцевом соединении |
1 мм |
9. Отклонение расстояния между центром узла и первым отверстием фасонок крепления распорок, раскосов и элементов диафрагм |
± 3 мм |
10. Угол между фактическим и проектным положениями фасонок для крепления раскосов и распорок |
1° |
Прочие конструкции и детали |
|
Отклонения в размерах: |
|
11. опорных столиков, служащих для установки монтажных механизмов и в привязке их размеров |
± 2 мм |
12. других деталей, предназначенных для производства монтажных работ (для подвески подмостей и др.) |
± 4 мм |
Примечание. Допускаемые отклонения в размерах проемов и деталей, направляющих для лифтов, устанавливаются в проекте. |
6.8. Стыковые сварные соединения листовых трубчатых мачт (включая монтажные) диаметром 1500 мм и более должны подвергаться контролю просвечиванием проникающими излучениями в размере 2% длины сварных швов, выполненных ручной или полуавтоматической сваркой, и в размере 1% длины сварных швов, выполненных автоматической сваркой.
Контроль производится преимущественно в местах пересечения швов.
6.9. Изготовленные конструкции мачт и башен не должны иметь отклонений выше указанных в табл. 8, 9 и 24 настоящей главы.
Монтаж
6.10. Приемка фундаментов должна производиться перед началом монтажных работ комплектно для каждой мачты или башни в соответствии с требованиями проекта, п. 1.104 (табл. 11) и табл. 25 настоящей главы.
При приемке проверяется наличие и геометрическое положение закладных деталей для крепления монтажных устройств.
6.11. Подливка опорных башмаков и заливка колодцев анкерных болтов в фундаментах башен должны производиться после выверки двух собранных и закрепленных секций башни. Подливка опорных фундаментных плит мачт должна производиться после их выверки до начала монтажа ствола мачты. Монтаж мачт на подлитых плитах и продолжение монтажа башен на подлитых башмаках разрешается производить только после достижения раствором подливки 50% проектной прочности. Работы по подливке оформляются актами.
Примечание. Части башмаков, не доступные заливке после установки первых секций, должны заполняться бетоном до монтажа секции.
Таблица 25
Наименование отклонения |
Допускаемое отклонение |
1. Расстояния между центрами фундаментов одной башни |
10 мм + 0,001 проектного расстояния при общей величине не более 25 мм |
2. Угол между фактическим и проектным направлением оси тяги анкерного фундамента мачты: |
|
к горизонту |
+0; - 4° |
в плане |
1° |
3. Отклонение опорных плит от проектной отметки: |
|
плиты центрального фундамента мачты и фундамента башни |
± 10 мм |
раздельно стоящие плиты башни (под поясами) |
1:1500 базы, но не более 5 мм |
6.12. Монтаж мачт, имеющих опорные изоляторы, должен производиться на временной опоре (предусмотренной в проекте) с последующим подведением изоляторов после монтажа всей мачты.
6.13. Перед началом подъема очередной секции мачты или башни заглушки труб в верхних фланцах поясов должны быть залиты битумом № 4 в уровень с плоскостью фланца, а соприкасающиеся плоскости фланцев - смазаны битумом той же марки. Выполнение этих работ должно оформляться актом.
6.14. Болты во фланцевых соединениях должны устанавливаться с двумя гайками.
6.15. Натяжные приспособления для оттяжек в мачтовых сооружениях и для раскосной решетки в башнях должны иметь паспорта, в которых приводятся документы о тарировке измерительного прибора.
6.16. Изготовление и испытание оттяжек должно производиться, как правило, на монтажной площадке. Канаты должны быть предварительно вытянуты в соответствии с требованиями п. 1.140 настоящей главы.
Оттяжки мачт в собранном виде или отдельными участками должны быть испытаны усилием, равным 0,5 разрывного усилия каната в целом.
В случаях, когда вытяжку и испытание канатов и оттяжек на монтажной площадке производить невозможно, допускается изготовление и испытание оттяжек производить на центральных базах и перевозить их к месту монтажа в бухтах с внутренним диаметром не менее 2,5 м для оттяжек из канатов диаметром до 42 мм и 3,5 м - для оттяжек из канатов больших диаметров.
6.17. Усилие монтажного натяжения в оттяжках мачтовых опор должно определяться по формулам:
при (5)
при (6)
где N - искомая величина натяжения при температуре воздуха во время определения;
N1 - величина натяжений при температуре воздуха плюс 40°С, приводится в проекте;
N2 - величина натяжения при температуре воздуха минус 40° С, приводится в проекте;
Nc - величина натяжения при среднегодовой температуре воздуха в районе установки мачты, приводится в проекте;
Тc - среднегодовая температура воздуха в районе установки, определяемая по данным гидрометеорологической службы;
Т - температура воздуха во время регулировки натяжения оттяжек мачт.
6.18. Выверка мачт и башен должна производиться без подвешенных антенн и при скорости ветра не более 25% расчетной.
Приемка работ
6.19. Отклонения законченных монтажом конструкций мачт и башен от проектного положения не должны превышать величин, указанных в табл. 26 настоящей главы.
Таблица 26
Наименование отклонения |
Допускаемое отклонение |
1. Смещение оси ствола и поясов башни от проектного положения |
высоты выверяемой точки над фундаментом
|
2. Смещение оси ствола и поясов мачты от проектного положения |
высоты выверяемой точки над фундаментом
|
3. Отклонение величины монтажного натяжения раскосов башен от проектного |
± 15% |
4 Отклонение величины предварительного (монтажного) натяжения оттяжек мачт от проектного |
± 8% |
5. Paзницa в величине натяжения оттяжек (из одного каната) одного яруса после демонтажа монтажного крана |
10% |
6.20. Помимо документов, перечисленных в п. 1.151 настоящей главы, при сдаче должны быть дополнительно представлены:
заводские сертификаты на стальные канаты, на сплавы для заливки втулок и на изоляторы;
акты на заливку битумом фланцев трубчатых поясов мачт и башен;
акты на изготовление и испытание оттяжек для мачтовых сооружений;
акты механических и электрических испытаний изоляторов;
ведомость геодезической проверки осей сооружения, а также осей элементов сооружения (поясов решетчатых мачт и башен);
ведомость замеренных предварительных (монтажных) натяжений оттяжек мачт и раскосов башен.
7. ДОПОЛНИТЕЛЬНЫЕ ПРАВИЛА ДЛЯ КОНСТРУКЦИЙ ГИДРОТЕХНИЧЕСКИХ СООРУЖЕНИЙ
7.1. Настоящие правила должны соблюдаться при изготовлении, монтаже и приемке стальных конструкций гидротехнических сооружений:
а) подвижных конструкций затворов (в том числе ворот судоходных шлюзов и доков) и разборных плотин:
б) подвижных конструкций сороудерживающих решеток, плавучих заграждений и прочих устройств, преграждающих доступ посторонним предметам к водопропускным отверстиям;
в) закладных частей затворов и сороудерживающих решеток;
г) стальных облицовок и экранов;
д) стальных трубопроводов гидроэлектрических и насосных станций;
е) уравнительных башен;
ж) причальных устройств на судоходных шлюзах и сооружениях гидроэлектрических станций;
з) балок и эстакад под механизмы.
Настоящие правила не распространяются на высоконапорные гидротехнические затворы из стальных отливок или сварной конструкции с большим количеством механической обработки, требующие повышенной точности пригонки подвижной конструкции к неподвижным (закладным) частям. Изготовление, монтаж и приемка таких затворов производятся по специальным техническим условиям.
7.2. При изготовлении, монтаже и приемке стальных конструкций, устанавливаемых или эксплуатируемых при расчетной температуре ниже минус 40°С, в отношении их механических деталей и деталей из резины должны соблюдаться требования государственного стандарта на машины, приборы и другие технические изделия, предназначенные для эксплуатации в условиях низких температур.
ИЗГОТОВЛЕНИЕ
7.3. Отклонения действительных размеров изготовленных конструкций от проектных не должны превышать величин, указанных в табл. 8, 9 и 27 настоящей главы.
Схема контрольных обмеров должна быть приложена к сертификату на изготовленную конструкцию.
7.4. На заводе должна производиться общая сборка следующих негабаритных конструкций: подвижных конструкций затворов всех типов, пазовых конструкций, элементов трубопроводов сложной формы (колен, переходных камер, разветвлений, компенсаторов и т.п.).
Таблица 27
Наименование отклонения |
Допускаемое отклонение |
Плоские и сегментные затворы |
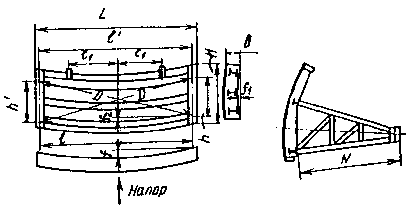
|
1. Отклонение длины L, высоты H, толщины В |
- (2 мм+0,001X), где за Х принимается соответственно или L, или B, или Н |
2. Отклонение расстояния l1 между осью затвора и осью подвеса |
- (1 мм +0,0003 l1) |
3. Разность между l и l' и между h и h', где l и l' - расстояния между геометрическими осями опорно-концевых стоек, измеренные по геометрическим осям соответственно нижнего и верхнего ригелей; h и h' - расстояния между геометрическими осями нижнего и верхнего ригелей, измеренные по геометрическим осям соответственно левой и правой опорно-концевых стоек |
3 мм |
4. Разность длин диагоналей |
0,001 D, но не более 10 мм |
5. Стрела кривизны обшивки и ригелей в горизонтальной плоскости f (только в сторону напора) |
0,0006 L |
6. То же, в вертикальной плоскости f1 (посередине каждой секции затвора) |
0,001 Н |
7. Стрела кривизны f2 ригелей в вертикальной плоскости |
0,001 L, но не более 15 мм |
8. Стрела кривизны f3 кромки ножа затвора с резиновым уплотнением |
± 3 мм |
9. Стрела кривизны f3 (кромки ножа затвора) без резинового уплотнения |
± 1 мм |

|
|
10. Тангенс угла отклонения линии, соединяющей оба конца кромки ножа, от перпендикуляра к оси затвора (см. примеч. 1) |

|
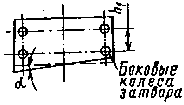
|
|
11. Винтообразность уплотняющего контура, измеряемая по плоскости установки уплотнений или по центрам отверстий под болты, крепящие уплотнения |
3 мм + 0,0002L |
12. Винтообразность конструкции затвора по контуру, не имеющему уплотнения |
6 мм + 0,0004L |
13 Отклонение длины N ног сегментного затвора |
±0,001 N, но не более 5 мм |
Ствоpки двустворчатых ворот
|
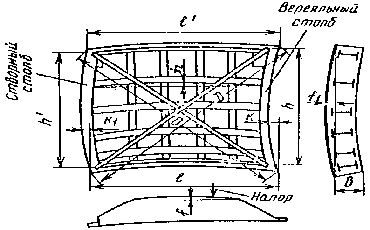
|
14. Отклонение толщины В, длины 1 и высоты h |
- (2мм+,001X), где за X принимается cоответственно или В, или l, или h |
15. Разность длин диагоналей |
0,001D, но не более 10 мм |
16. Стрела кривизны К вереяльного столба и K1 створного столба (в любой плоскости) |
0,001 высоты столба, но не более 10 мм |
17. Стрела кривизны f обшивки и ригелей и горизонтальной плоскости (только в сторону напора) |
0,0006 l |
18. Стрела кривизны f1 обшивки в вертикальной плоскости посередине створки (только в сторону напора) |
0,001 h |
19. Стрела кривизны f2 ригелей в вертикальной плоскости |
0,001 1 но не более 10 мм |
Откатные ворота |
|
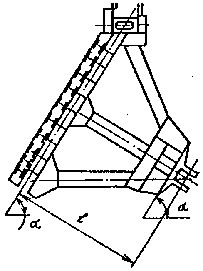
|
|
20. Отклонение расстояния l, определяющего положение опорно-ходовых частей |
± 0,001l |
21. Отклонение тангенса угла наклона  |
± 0,001 |
|
|
Трубопроводы |
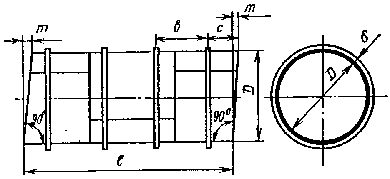
|
22. Отклонение длины наружной окружности на концах обечайки |
± 0.3 , но не более 10 мм |
23. Смещение кромок в стыках |
0,1 , нo не более 3 мм (для сталей высокой прочности в продольных стыках - не более 2 мм) |
24. Разность между шприцами листов, входящих в состав одной обечайки негабаритного трубопровода или уравнительной башни |
2 мм |
25. Местные зазоры между внутренней кромкой кольца жесткости (или опорного) и шаблоном длиной 1500 мм |
2 мм на длине не более 200 мм |
26. Отклонение длины l |
|
Прямого звена или обечайки |
(2 мм+0,001l)
|
фасонного звена или обечайки |
(2 мм+0,0005l)
|
27. Отклонение расстояния: от кольца жесткости (или опорного) до края обечайки с |
|
между кольцами жесткости b |
30 мм
|
от кольца жесткости (или опорного) до края обечайки с |
15 мм
|
28. Зазор между боковой поверхностью кольца жесткости (или опорного) и стальной линейкой длиной 1 м |
3 мм |
29. Тангенс угла отклонения кольца жесткости (или опорного) от проектного положения |
± 0,005 |
30. Косина торцов обечаек т |
3 мм |
31. Отклонение зазоров между внутренней и наружной поверхностями звеньев компенсатора трубопровода |
|
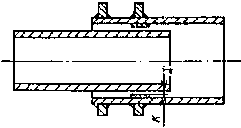
|
+0,5К
-0,2К |
Закладные части |
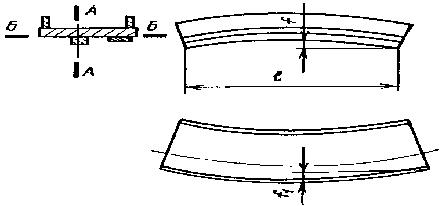
|
32. Стрела кривизны закладных частей, состоящих из отдельных сварных или прокатных профилей с необработанными плоскостями: |
|
для элементов, расположенных в пределах рабочей зоны:: |
|
f - в плоскости а - а действия нагрузки затвора |
0,001l, но не более 4 мм |
f1 - в плоскости б - б, перпендикулярной действию нагрузки от затвора для элементов, расположенных вне пределов рабочей зоны затвора |
0,002l, но не более 5 мм |
f - в плоскости а - а |
0,002l, но не более 6 мм |
f1 - в плоскости б - б |
0,002l, но не более 6 мм |
33. Стрела кривизны закладных частей, состоящих из отдельных сварных или прокатных профилей с обработанными плоскостями, независимо от зоны расположения закладных частей: |
|
f - в плоскости а - a |
0,0005l, но не более 1 мм |
f1 - в плоскости б - б |
0,0001l, но не более 3 мм |
34. Смещение оси цилиндрической поверхности рельса от оси пути |
± 2 мм |
35. Местные углубления на рабочей поверхности рельса для скользящих затворов |
0,3 мм, два углубления на 1 м длины рельса |
36. Местные сквозные зазоры между квадратом рельса для скользящих затворов и закладной частью (см. Примеч. 2) |
Один зазор до 0,1 мм длиной не более 100 мм на 1 м длины рельса |
37. Местные несквозные зазоры между квадратом рельса для скользящих затворов и закладной частью (см. примеч. 2) |
Два зазора до 0,3 мм длиной не более 150 мм на 1 м длины рельса |
38. Винтообразность пазовых конструкций закладных частей затвора, измеряемая но концам отправочного элемента |
0,001 длины |
Плоскостные облицовки пазов затворов, не соприкасающиеся с уплотняющими элементами затвора |
|
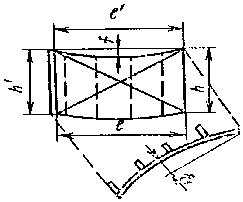
|
|
39. Стрела кривизны f в плоскости облицовки при соединении: |
|
внахлестку |
0,002l, но не более 10 мм |
встык |
2 мм |
40. Стрела кривизны f, из плоскости обшивки |
0,002l и 0,002h, но не более 10 мм |
41. Разность между размерами облицовки, измеряемыми между гранями l и l' или между h и h' |
2 мм |
42. Разность длин диагоналей при соединении: |
|
внахлестку |
10 мм |
встык |
2 мм |
43. Местные вмятины (на отправочный элемент) |
Три вмятины глубиной не более 10 мм |
Плоскостные облицовки и забральные балки, соприкасающиеся с уплотняющими элементами затвора |
|
44. Стрела кривизны из плоскости облицовки, измеренная в любом направлении. для плоскостей: |
|
необработанных |
+ 3 мм на каждый 1 м длины, но не более +6 мм на всю длину |
обработанных |
+ 1 мм на каждый 1 м длины, но не более +3 мм на всю длину |
45. Местные вмятины на плоскостях: необработанных (на отправочный элемент) |
Две вмятины глубиной до 5 мм |
обработанных |
Не допускается |
Примечания: 1. На затворах с соединенными секциями размер h1 измеряется между осью верхнего и нижнего боковых колес крайних секций.
2. Измерение .зазоров по поз. 36 и 37 производится до сварки после плотного прижатия рельса к закладным частям. |
Таблица 28
Наименование отклонения |
Допустимое отклонение |
Колеса |
|
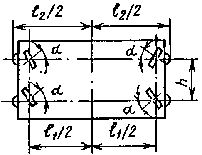
|
|
1. Отклонение четвертого колеса от плоскости, касающейся трех других колес *: |
|
а) в затворах без продольных связей при расчетном пролете l1: |
|
до 5 м |
± 0,001 l1 |
свыше 5 до 10 м |
± (3 мм+0,0004 l1) |
свыше 10 м |
± (5 мм+0,0002 l1) |
б) в затворах с продольными связями при расчетном пролете l1: |
|
до 5 м |
± 0,0007 l1 |
свыше 5 до 10м |
± (2,5 мм+0,0002 l1) |
свыше 10 м |
± (3 мм+0,00013 l1) |
2. Тангенс угла наклона геометрической оси вращения колеса к горизонтальной оси затвора |
± 0,003 |
3. Отклонение расчетного полупролета l1/2 (расстояние от средней плоскости колес до оси затвора) |
±(1 мм+0,00015 l1) |
4. Отклонение расстояния h между осями колес, расположенных на одном и том же конце затвора |
±(2 мм +0,0007h) |
5. Отклонение расстояния l2/2 от кpайней точки рабочей поверхности торцевых (боковых) колес до оси затвора |
±(1 мм+0,00015 l2) |
6. Отклонение по высоте собранной балансирной тележки |
+3 мм |
Полозья с древесным слоистым пластиком |
|
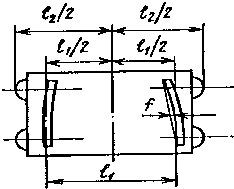
|
|
7. В затворах с полозьями на всю длину опорно-концевых стоек отклонение одного конца рабочей поверхности полоза от плоскости, касающейся трех других концов рабочих поверхностей полозьев |
По поз. 1 настоящей таблицы |
8. В затворах с четырьмя короткими полозьями отклонение середины рабочей поверхности одного полоза от плоскости, проходящей через середины рабочих поверхностей трех других полозьев |
То же |
9. Отклонение расчетного полупролета l2/2 (расстояние от средней плоскости полозьев до оси затвора) |
±(1 мм+0,00015 l1) |
10. Сквозные зазоры между соприкасающимися поверхностями обоймы полоза и стальной конструкции затвора: |
|
при необработанных поверхностях

|
1 мм на отдельных участках длиной не более 200 мм и при суммарной длине таких участков не более 20% всей длины полоза
|
при обработанных поверхностях |
0,3 мм на отдельных участках длиной не более 100 мм и при суммарной длине таких участков не более 15% всей длины полоза
|
11. Несквозные зазоры между соприкасающимися поверхностями обоймы полоза и стальной конструкции затвора: |
|
при необработанных поверхностях
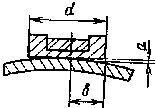
|
0,5 мм, 0,1d при суммарной длине зазоров не более 50% всей длины полоза
|
при обработанных поверхностях |
0,3 мм, 0,1d при суммарной длине зазоров не более 25% всей длины полоза
|
12. Зазор между рабочей поверхностью полоза и линейкой длиной 1 м |
1 мм |
13. Стрела кривизны рабочей поверхности полоза в плоскости, перпендикулярной ей |
1 мм на 1 м, нo не более 2 мм на длину полоза |
14. Уступы в стыках брусков древесного слоистого пластика на рабочей поверхности полоза |
0,2 мм |
Опорные части двустворчатых ворот |
|
15. Смещение оси паза под вкладыш в упорной подушке |
± 3 мм |
16. Тангенс угла наклона вертикальной оси упорной подушки |
0,003 |
17. Смещение отверстий для смазки пяты, расположенных в ригеле и надпятнике |
0,1 диаметра отверстия, но не более 2 мм |
Плоские затворы на одной подвеске |
|
18. Наклон вертикальной геометрический оси свободно подвешенного затвора |
1 мм на 1м высоты затвора |
*Если габаритный затвор снабжен балансирными тележками, то указанные отклонения относятся к положению центра опорных поверхностей шарнирных катков балансирных тележек. |
Объем и последовательность общей сборки производятся в соответствии с проектом.
7.5. Габаритные конструкции поставляются заводом-изготовителем в полностью законченном виде, с установленными на них опорно-ходовыми и уплотняющими устройствами.
Балансирные тележки затворов допускается транспортировать отдельно.
Опорно-ходовые узлы и комплектующие детали негабаритных конструкций должны быть приняты с рассверловкой крепежных отверстий на проектный диаметр при общей сборке.
Допускаемые отклонения от проектного положения при установке опорно-ходовых устройств должны приниматься по табл. 28 настоящей главы.
7.6. Анкерные детали на закладных частях и облицовках заводом-поставщиком не устанавливаются, но отгружаются одновременно с конструкциями.
7.7. Стыки резиновых уплотнений выполняются горячей вулканизацией.
7.8. На отправочных элементах конструкций должны быть указаны места строповки и центра тяжести; конструкции должны быть снабжены устройствами для строповки и кантовки.
7.9. Механически обработанные и не окрашиваемые поверхности опорно-ходовых и закладных частей должны быть защищены от коррозии и предохранены от повреждений на время транспортировки и монтажа.
Сварка при изготовлении и монтаже
7.10. Сварные соединения в зависимости от их конструктивного исполнения и напряженного состояния разделяются на I, II и III категории.
Категория сварного соединения указывается на рабочих чертежах в условном обозначении шва последним знаком римской цифрой. При отсутствии такого указания соединение контролируется как соединение III категории.
7.11. Механические свойства сварных соединений I и II категории должны быть подтверждены испытаниями контрольных пластин, заваренных каждым сварщиком в начальный период сварки изделия или партии одинаковых изделий. Сварка контрольных пластин должна соответствовать требованиям п.1.60 настоящей главы.
7.12. Временное сопротивление сварного соединения при растяжении должно быть не менее нижнего предела временного сопротивления основного металла.
Ударная вязкость на образцах с надрезом в околошовной зоне на расстоянии 2 мм от границы сплавления и с надрезом по оси шва должна быть не менее 8 кгс·м/см2 при температуре испытания плюс 20°С и не менее 3 кгс·м/см2 при температуре испытания минус 40°С. Образцы для определения ударной вязкости вырезаются со стороны подварочного шва.
Для металла толщиной 40 мм включительно угол изгиба сварного соединения вокруг оправки с радиусом, равным толщине металла, определяемый на образцах с поперечным расположением шва, должен быть не менее 120° для углеродистых сталей и 100° для низколегированных сталей. Образцы для испытаний на изгиб при толщине металла более 40 мм сострагиваются со стороны основного шва до толщины 40 мм. При испытании на изгиб подварочный шов должен находиться в растянутой зоне.
Твердость металла шва и околошовной зоны, измеренная алмазной пирамидой, должна быть не более 350 единиц.
7.13. Физические методы контроля сварных соединений (ультразвуковая дефектоскопия, просвечивание проникающими излучениями и др.) применяются в следующем объеме:
а) по всей длине для соединений I категории;
б) не менее 50% длины швов для соединений II категории;
в) на участках, где на основании наружного осмотра предполагается наличие внутренних дефектов, - для соединений III категории.
Примечания: 1. При контроле швов I и II категории ультразвуком достоверность заключения о качестве должна подтверждаться выборочным просвечиванием проникающими излучениями всех участков шва с признаками дефектов.
2. Способы и нормы физического контроля соединений из специальных сталей (высокопрочных, нержавеющих, жаропрочных) и соединений литья с прокатом устанавливаются проектом.
7.14. Швы I категории с внутренними дефектами, выявленными физическими методами контроля, в виде трещин, непроваров и скоплений пор должны быть исправлены и повторно проверены. Единичные, не выходящие на поверхность шва шлаковые включения и газовые поры диаметром не более 3 мм и глубиной не более 10% от толщины металла допускаются, если они расположены один от другого на расстоянии не менее 100 мм и от концов шва на расстоянии не менее 200 мм.
Дефекты в сварных соединениях II и III категории по размерам и протяженности не должны превышать норм, указанных в разделе 1 настоящей главы.
Антикоррозионная защита при изготовлении и монтаже
7.15. Габаритные конструкции грунтуются и окрашиваются на заводе-изготовителе. Негабаритные конструкции разрешается на заводе-изготовителе только грунтовать, а окрашивать их следует после монтажа.
7.16. Поверхности конструкций, подлежащие обетонированию, очищаются от окалины и ржавчины на заводе-изготовителе, окончательная очистка производится на монтаже непосредственно перед бетонированием.
МОНТАЖ
Хранение и укрупнительная сборка
7.17. Резиновые уплотнения, установленные на конструкциях, должны быть окрашены мелом, разведенным на воде с клеем, и защищены от воздействия солнечных лучей, а поверхности древесного слоистого пластика покрыты слоем солидола и защищены от повреждения. Детали, поставляемые отдельно от конструкций, должны храниться в закрытых складах.
7.18. Отклонения укрупненных на монтаже конструкций от проекта не должны превышать величин, приведенных в табл. 27 и 28 настоящей главы.
7.19. Стыки резиновых уплотнений выполняются горячей вулканизацией.
7.20. Укрупнительная сборка и сварка закладных частей пазов плоских затворов должны производиться в кондукторах.
7.21. На укрупненные конструкции должна быть составлена схема контрольных замеров.
Закладные части
7.22. Разбивочные оси должны быть закреплены в натуре таким образом, чтобы положение закладных частей можно было проверить после бетонирования.
7.23. Приварка закладных частей к выпускам арматуры должна быть выполнена с применением прямых соединительных деталей, установленных по направлению действия усилий при бетонировании, швами длиной не менее 60 мм, причем замыкающие стыки раскреплений должны быть сделаны внахлестку.
Раскрепление закладных частей должно обеспечивать неизменяемость их положения при бетонировании. Допускаемые отклонения от проектного положения при установке порога и забрала должны приниматься по табл. 29, путей плоских затворов - по табл. 30, облицовок и армировок пазов - по табл. 31.
Таблица 29
|
Допускаемые отклонения, мм |
Наименование отклонения |
порога
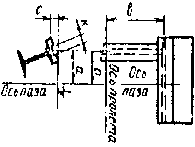
|
забрала
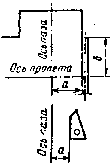
|
1. Отклонение расстояния a от оси закладных частей до оси паза |

|
-- |
2. Отклонение расстояния a oт оси закладных частей до оси паза при баббитовой заливке на пороге |
+0,05К (К - ширина баббитовой заливки порога) |
-- |
3. Отклонение расстояния а от оси паза до уплотняющей плоскости закладных частей |
-- |
±4 |
4 Отклонение расстояния b до оси пролета |
±5 |
±5 |
5 Общее изменение высотного положения (примеч. 2) |
±10 |
±10 |
6. Винтообразность с |
±3 |
±3 |
7. Oтдельные местные неровности (впадины и выпуклости) на paбoчeй поверхности закладных частей |
±2 |
±2 |
8. Уступы в стыках |
1 |
1 |
9. Превышение одного конца закладной части над другим при длине: |
|
|
до 10 м |
1 |
5 |
свыше 10 м |
2 |
7 |
10. Стрела кривизны в вертикальной плоскости на длине. 5м |
±4 |
±4 |
11. Стрела кривизны в вертикальной плоскости на длине 5 м при баббитовой заливке на пороге |
±2 |
-- |
Примечание. Измерения забрала по поз. 5 производятся от порога до закладных частей забрала. |
7.24. Если бетонирование не будет произведено в течение трех суток после приемки закладных частей, то правильность их положения должна быть проверена повторно с тем, чтобы указанный срок был выдержан.
Трубопроводы
7.25. Катки опор трубопровода должны соприкасаться по всей длине со всеми опорными плитами. Установка катков на опорные плиты должна производиться с учетом наблюдаемой в это время температуры.
Устройства для обогрева затворов и образования майн
7.26. Стальные конструкции электрообогрева, примыкающие к закладным частям, должны быть установлены и приняты одновременно с ними.
7.27. Расстояние от токонесущих элементов электрообогрева до арматуры и других металлических частей должно быть не менее 75 мм.
Таблица 30
Допускаемые отклонения путей, мм |
рабочих |
обратных |
торцевых |
Боковых |
колесных затворов |
скользящих затворов |
с полозьями из ДСП-Бгт |
|
|
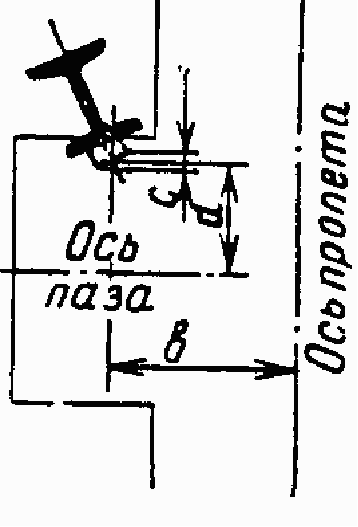
|
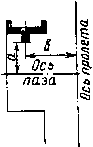
|
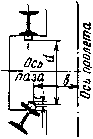
|
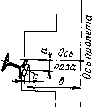
|
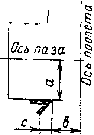
|
рис.1 |
рис.2 |
рис.3 |
рис.4 |
рис.5 |
Таблица 30
Наименование |
Допускаемые отклонения путей, мм |
отклонения |
рабочих |
обратных |
торцевых |
Боковых |
|
См.рис.1 |
См.рис.2 |
См.рис.3 |
См.рис.4 |
См.рис.5 |
1. Отклонение расстояния а**** от рабочей поверхности закладных частей до оси паза*: |
|
|
|
|
|
в рабочей зоне |
+3
-1 |
+3**
-1 |
- |
±5 |
+5
-2 |
вне рабочей зоны |
+5
-2 |
+5**
-2** |
-- |
±5 |
+7
-2 |
2. Отклонение расстояния b**** от оси закладных частей до оси пролета*: |
|
|
|
|
|
в рабочей зоне |
±3 |
±3 |
±5 |
+5
-3 |
±5 |
вне рабочей зоны |
±5 |
±5 |
±3 |
+5
-3 |
±5 |
3. Отклонение расстояния d**** между рабочими и обратными путями: |
|
|
|
|
|
в рабочей зоне |
-- |
-- |
+5
-2 |
-- |
-- |
вне рабочей зоны |
-- |
-- |
+8
-2 |
-- |
-- |
4. Винтообразность с: |
|
|
|
|
|
в рабочей зоне при ширине рабочей поверхности: |
|
|
|
|
|
до 100 мм |
±1 |
- |
±2 |
±2 |
±2 |
более 100 мм |
±2 |
- |
±3 |
±3 |
±3 |
вне рабочей зоны допуски увеличиваются на |
2 |
-- |
2 |
2 |
2 |
5. Местные неровности на рабочей поверхности: |
|
|
|
|
|
в рабочей зоне |
±1 |
±0,1 |
±2 |
±2 |
±2 |
вне рабочей зоны |
±3 |
±1 |
±2 |
±3 |
±2 |
6. Уступы в стыках ***: |
|
|
|
|
|
в рабочей зоне |
1 |
0,2 |
1 |
1 |
1 |
вне рабочей зоны |
2 |
0,2 |
2 |
2 |
2 |
* Измерение расстояний до закладных частей производится по оси рабочей поверхности.
** Разность между двумя соседними по высоте промерами а не должна превышать 1 мм.
*** Уступы в стыках должны быть сглажены, выступающие острые кромки не допускаются.
**** Промеры производятся через метр по высоте закладной части, но не менее чем в трех местах на одном монтажном элементе. |
Предыдущая часть |
К оглавлению
| Следующая часть
|